How Cables Are Made - Step 5: Braiding
When producing cables and wires, every little detail counts. In the fifth part of our series, you will learn how braids around cables are made and what purposes they serve.
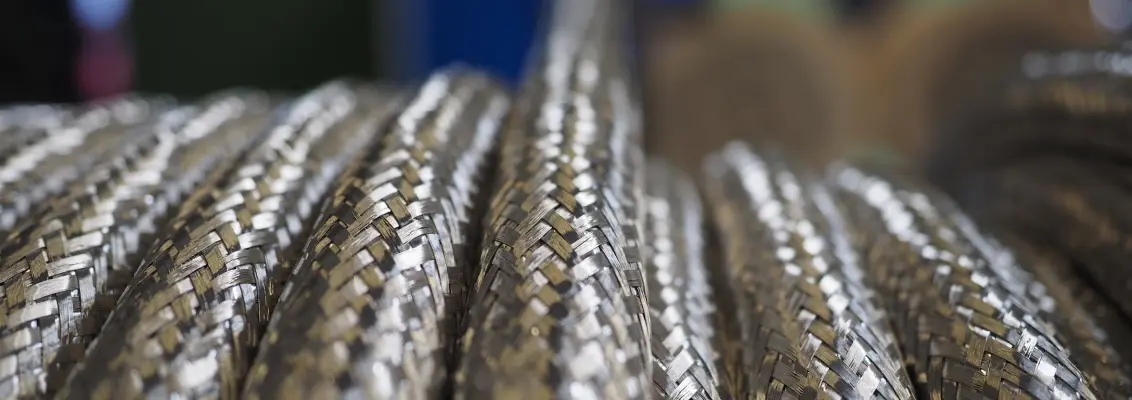
After individual cores have been stranded into cables, about 70 percent of these cables end up at the braiding station. Here, 35 braiding machines are waiting to put their spools into action and place braids around the cables. Braiding serves one of two purposes: it either guarantees electromagnetic compatibility (EMC) or protects the cable from mechanical stress. Braids that are made from bare or tinned copper wires are normally used to provide immunity to electromagnetic interference. Depending on the application, they prevent the escape of radiation from the cable and/or stop undesired signals from penetrating it. Both cases can lead to plant failure and outages. Stabilising steel, yarn or textile braids protect cables from external loads. A few examples of their benefits in everyday applications include resistance to shards and rodent bites, protection when a cable is stepped on, and strain relief when hoisting equipment.
The braiding machines at the Windsbach plant have been designed to build braided screens (C-screens) around cables with diameters from 1.9 to 75 millimetres. Alongside these machines, wrapping machines are used for so-called wrapped screens (D-screens). Wrapped screens are made by placing copper wires around the cable. The result is a torsion-tested cable with 95 to 100 percent coverage. Braided screens, on the other hand, easily withstand bending and unbending cycles in drag chains and have about 85 percent coverage. Generally speaking, the following applies to braiding: the greater the pitch, i.e., the angle of the individual braiding wires, the more flexible the cable. The smaller the braiding angle, the thicker the braid and hence the better the protection.
What does “armouring” mean?
Tensile and compressive loads can cause mechanical damage to cables and wires. The armour, also known as reinforcement, forms a protective layer around the core stranding to fully preserve the functionality of the cables and wires. It is usually made of either a steel wire mesh, round or flat steel wires or steel tapes, or a combination of these materials.
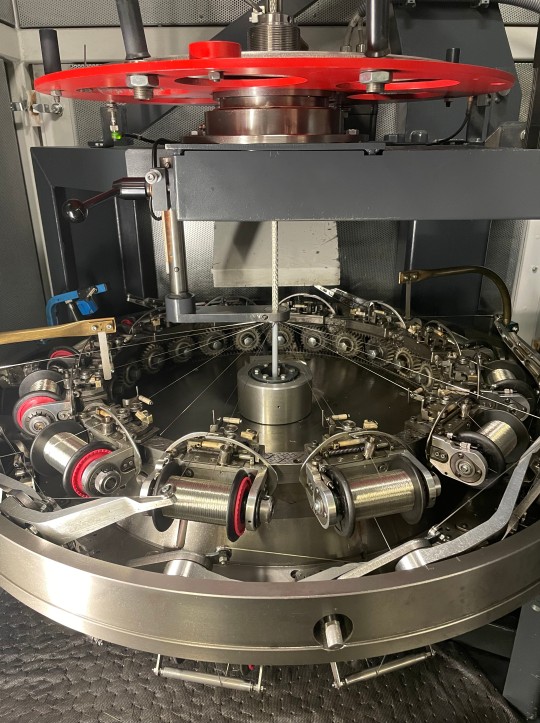
Ask the expert
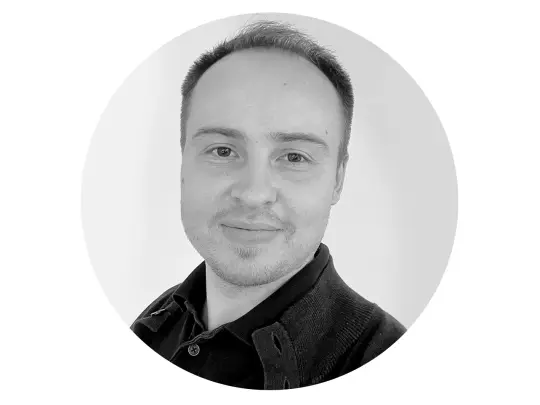
Mr. Schneider, from your point of view, what is important in the braiding process?
Firstly, the material: the wire used is essential for the shielding. For optimal shielding and flexibility, we most often use copper coated with tin, which offers improved corrosion protection. The quality of the process itself is also important - this starts with the even winding of the braiding coils to minimise wire cracks in the braider. And last but not least, we rely on modern machinery with suitable tooling, where we can apply high-quality braids and taping and monitor this process.
Part of this process requires the regular replacement of the braiding bobbins. What needs to be taken into account during this step?
Before inserting the spool, it is important to check the wire and the spool for mechanical damage and ensure that the wire bundle is running optimally. After insertion, all seals must be checked again. The wire bundle must be guided precisely over the rollers of the spool carrier and possibly the thread carrier and braided into the braid. We then have to process and inspect the braided area - this requires a lot of precision. Only then can production be restarted.
What are the different requirements for processing various braiding materials?
Every material has a certain tensile stress. That's why we have to adjust the braking and pull-off force on the bobbin carriers according to different materials and plaits. We also choose the appropriate braider depending on the material used.