“Enormous opportunities, many of which we are still completely unaware of”
Megatrend industrial automation: experts discuss opportunities and challenges
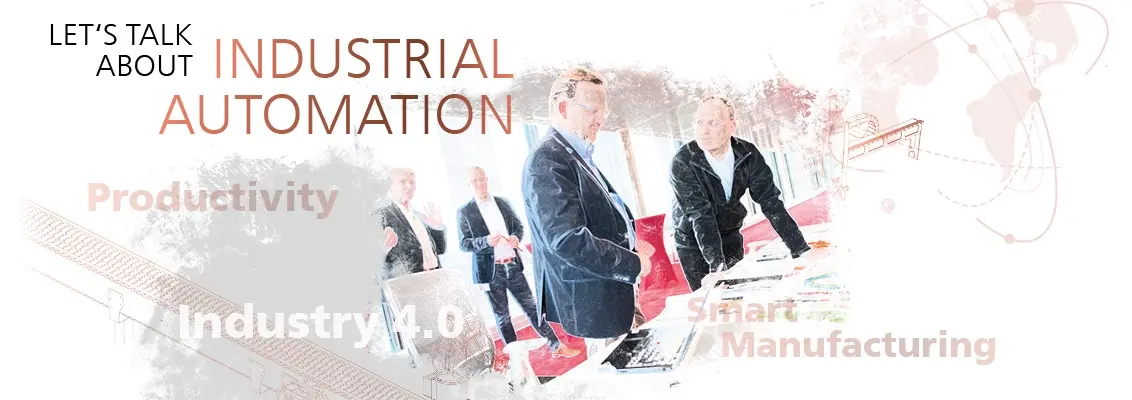
Whether in production, assembly, material handling or logistics: Automation is being integrated into more and more processes across all industries and areas of business and it’s is changing them from the bottom up. Cables and wires are like a nervous system: When required, they transmit signals, data and power from the sensor via the controller to the management level. In an expert discussion, we looked closely at the challenges facing industrial automation as well as likely future developments and trends in this exciting area.
The term “industrial automation” is a very broad one and covers many sub-disciplines. What’s your definition of industrial automation?
Martin Schleef: Imagine a machine or a set of linked machines which repeatedly performs specific tasks at high speed. Simply put, industrial automation is about how to control these machines, i.e., how to start them, stop them in the middle of production or make improvements to them. The most relevant benchmark here is the so-called overall equipment effectiveness or OEE. This metric reflects the utilisation of equipment relative to production time, and converts the availability, performance and quality levels into easy-to-visualise ratios. At the Fraunhofer IPA, we investigate how OEE can be improved using sensor technology, artificial intelligence and other technologies.
Matthias Eick: As I see it, the goal of industrial automation is to automate processes with high repeatability accuracy and eliminate the need for human involvement. Such processes are no longer the exclusive domain of the shop floor: there are many other areas also benefiting from the advancements in automation. There is now an abundance of smaller, more powerful, and easier-to-use technical tools on the market.
Steffen Quadt: The term is no longer exclusive to manufacturing. Agriculture is also a type of industry. In my opinion, the primary goal of industrial automation is to improve productivity. This can be done through technology but also through new methods and approaches. The same technology can achieve completely different results, depending on how it’s deployed.
Frank Sangel: In addition to productivity, automation is also about relieving people of monotone and tiresome tasks which improves process safety.
Schleef: That’s right. We distinguish between different drivers of automation, such as quality in the form of repeat accuracy, for example, or ergonomics and staff availability.
Eick: Automation doesn’t just mean making processes more productive but optimising the use of resources. Machines in processing industries, for example, can schedule and use material a lot more efficiently with the help of computed models.
The automation of industrial processes is an interaction of diverse components. Based on your understanding, what counts as automation technology?
Quadt: We view automation technology from both a vertical and a horizontal perspective. The vertical perspective is the famous automation pyramid that’s divided into different levels: Right at the bottom on the so-called component level are the actuators and sensors; above them are the control level, manufacturing management technology and enterprise planning management level. The goal is to always automate in a structured manner from the bottom up. This approach gives a schematic view of the automation. There is also the horizontal perspective, the so-called product life cycle. This starts with the requirements definition in the development phase, i.e., long before manufacturing begins. Moreover, it carries on until there is a successor or the product is discontinued and includes the supply of spares parts. The horizontal perspective is becoming increasingly relevant in the light of issues such as sustainability, energy and resource efficiency.
Eick: It’s almost impossible for most users to see things in this all-embracing way. In practice, it’s more likely a case of “I want to make a certain product, so I have to adapt my processes accordingly”.
Quadt: And for exactly this reason, the evolution of automation technology is far from over. Artificial intelligence and predictive algorithms will be used a lot more in future to analyse and optimise operations. The two-dimensional view we now have will probably extend into multiple dimensions.
Industry 4.0, IIoT and Big Data: Industrial automation is slowly but surely moving into IT as well. What possibilities and risks do you see arising from this?
Schleef: At the moment we are collecting lots of data but do are not doing anything with it, and this is a problem. The question is: who does the manufacturing data belong to? Does it belong to the manufacturing company or the machine manufacturer? Sharing data also means surrendering sensitive information which many companies are reluctant to do.
Jürgen Berger: And the IT in small and mid-sized enterprises isn’t usually as good as it should be. The implementation of new technologies simultaneously opens the door to external attacks, so companies have to start protecting themselves from these as well. Many are worried about this vulnerability when they introduce automation because cyber-attacks can halt production, for example. It’s less about individual processes though, than a fundamental willingness to accept this risk.
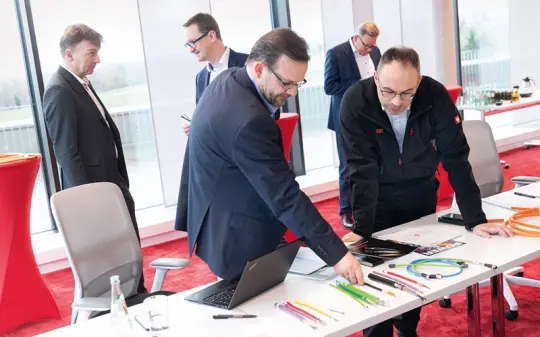
Eick: IT security is the fastest changing area in industrial automation. Companies can’t treat this as a one-off topic. Instead, they have to keep their eyes on the ball and they need help from outside to do this.
Quadt: That’s true. Cyber security needs lots of highly qualified and skilled persons. But when it’s in place, automation opens enormous opportunities, many of which we are still completely unaware. There are connections we don’t see yet because they’re so complex. Advanced algorithms and machine learning put us in a position to better understand the complexity and recognise patterns that were previously unknown.
For a long time, automation was only for large companies. How can it be made accessible to small and mid-sized ones as well?
Schleef: The level of automation does tend to be higher in large companies than in small and mid-sized ones. But failure to invest in automation will eventually be a problem, for example, when productivity suffers and a company loses its competitive edge. I see enormous potential here for robotics, in particular, cobots: Application possibilities are literally exploding, and robots are getting cheaper and easier to use. Most people don’t realise how simple it is to program a cobot. And through “imitation learning” robots teach themselves a lot too.
Quadt: The first hurdle many companies face are the high costs. These are unavoidable but they amortise themselves quickly as operators are keen to maximise usage of their machines. The best machine is not necessarily one optimised to do one single job quickly and efficiently. One that is flexible enough to do several jobs might be more appropriate.
Schleef: That’s very true. Even large manufacturers, for example in the car industry, are investing more and more in innovative concepts rather than highly specialised assembly lines. One of these concepts is so-called matrix production where products take flexible paths between production cells, allowing better mapping of diverse variants. This approach also is interesting for small and mid-sized enterprises manufacturing smaller quantities.
Eick: The flexibility of Industry 4.0 – where batch sizes as small as 1 are economically viable – inevitably comes at the cost of slightly lower efficiency. Small and mid-sized enterprises don’t need to redesign the whole shop floor all at once. Instead, they can start with an island solution with decentralised drive technology or replace individual systems and components. This allows them to gradually familiarise themselves with automation.
Schleef: Many companies have no idea how to optimise their machine pool beyond its already existing level of automation – be it through further digitalisation, extended recording of measurement and quality data or artificial intelligence. But if they do, it opens many new doors, even for systems thought to be already working at peak performance. There are public support programmes, such as so-called Quick Checks which companies can use to get their factories analysed and assessed over the course of a few days.
Sangel: The time and cost of connecting and wiring up automation technology used to be immense which was off-putting to many machine builders. These days though, everything today is pre-configured and assembled which makes it much easier.
Industrial automation is always associated with job losses. Is this true?
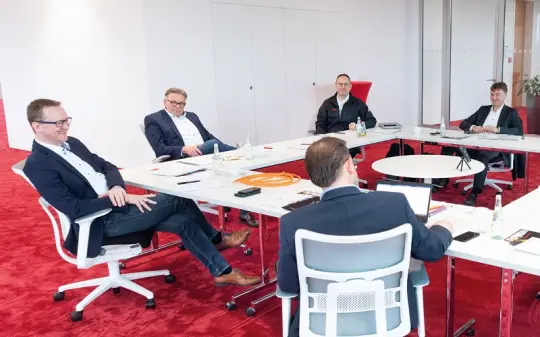
Schleef: Some people like to claim the goal of automation is to reduce costs by cutting down on staff. But this argumentation is unconvincing: There are many professions where companies are finding it difficult to recruit anybody at all and this is almost forcing them to go down the automation path. Rather than being a threat, automation is a guarantee of jobs. For many activities would no longer be possible if automation didn’t make up for the lack of staff.
Quadt: Automated industries also need qualified professionals, sometimes more than before. The job specification is only different. The skilled trades industry is in a similar situation. In my opinion, politicians must do more here to address this shortage.
Berger: That’s exactly what I think. Here in Germany for example we depend on immigration so we should make more of an effort to integrate foreign skilled personnel. There’s a lot of catching up to do.
Eick: But the skills shortage is not unique to Germany. We’re also finding it more and more difficult to recruit suitable people for several jobs in other countries, for example, in Eastern Europe.
Quadt: Automation has another major plus point: it removes the need for people to do tiring, monotonous or dangerous work that nobody wants to or is allowed to do any more. We should use people’s other strengths, for example, their flexibility. As a society, it’s our responsibility to encourage qualifications and professional development rather than preserve outdated jobs and activities. We don’t depend on raw materials for our prosperity in Central Europe but on technologies and our ability to develop and exploit them.
In future, companies will have to make their production and logistics both smarter and greener, i.e., more sustainable. How can automation help here?
Sangel: There are injection moulding machine manufacturers, for example, who now use servomotors instead of hydraulic power to hold their tools. The big advantage of this is that the servomotor only needs energy when it’s moving, while a hydraulic system needs power all the time. Large manufacturers often use dozens of these machines. The energy saving potential is enormous. There are studies which show that replacing pneumatic and hydraulic systems with electrical automation technology reduces power consumption by ten per cent. The production of compressed air is very energy-intensive, and in addition there are all the leakages. Moreover, small servo drives are considerably easier to automate than compressed air cylinders.
Eick: When it comes to cables, hybrid ones area smart way of saving resources. Power and data are combined in one cable. This means I only need one instead of two cables which saves on manufacturing materials. In addition, there are lots of other components such as drag chains and couplers which can be dimensioned smaller and more efficiently. Hence, we’re contributing to a greener environment with our products.
Quadt: Machinery and components with a long service life also contribute to sustainability. A gear box, for example, can be used for several decades. Electronic equipment on the other hand tends to become obsolescent more quickly. So, the aim must be to develop strategies for improving service life, for example, by updating or upgrading rather than replacing devices.
Sangel: And this brings us to the topic of retrofits which is also a step towards better sustainability. In machine-tool building, for example, it’s worth modernising old machinery as the mechanical parts still have plenty of life in them. When the automation technology is replaced, the result is often a much more efficient machine at a fraction of the cost of a new one.
Quadt: We have to develop automation technology in future that supports a circular economy. Raw materials such as magnets and rare earths are expensive. Some of them are very difficult to source and others can only be found in crisis areas. Therefore it’s becoming more important to think about processes such as the dismantling and recycling of these materials as early on as the design phase of a new product.
Many sectors in industry are now completely automated. Where do you still see possibilities and which new applications do you have in mind for the future?
Berger: Predictive maintenance, i.e., the maintenance of machinery and equipment through condition monitoring and data analyses, is a big topic. In theory, this can already be done today, but in practice it isn’t, and often for simple reasons: for example, because the relevant measurement data hasn’t been defined. Sometimes there are difficulties preparing the data. Or there might be problems defining the evaluation criteria, something which is very complex and has to be done for each individual application.
Quadt: There are so many causalities connected with machinery and equipment, some of which we don’t even know about. The only way forward here is to create a measurement culture and record as many measurable parameters as possible. Smart algorithms can work out later on which of them are relevant. It has to be clearly explained to the customer: we have an idea but not the solution! We have to work together to find it. Many companies are aware of condition monitoring and predictive maintenance, but a key part is often missing still.
Schleef: The many possibilities for automation in the assembly shop shouldn't be forgotten. Here, many jobs are still done by hand which cobots could do. Skilled trade activities, such as those in the building industry, are seeing massive automation as well. Another trend are digital tools such as data glasses and HoloLens glasses which, among other things, remotely support employees during commissioning or servicing by providing them with information and instructions.
Quadt: In any case, humans and machines are moving closer and are better connected with each other. Maintenance in a semi-virtual environment is an example of this. Many activities can be performed quicker, more effectively and with fewer errors. Virtual designs of machinery and equipment already exist, for example, but in future it will be possible to commission them virtually as well. Optimisation possibilities are being discovered even before equipment has been physically built. I’m convinced that the development of industrial automation is still very much in its infancy.
About the people
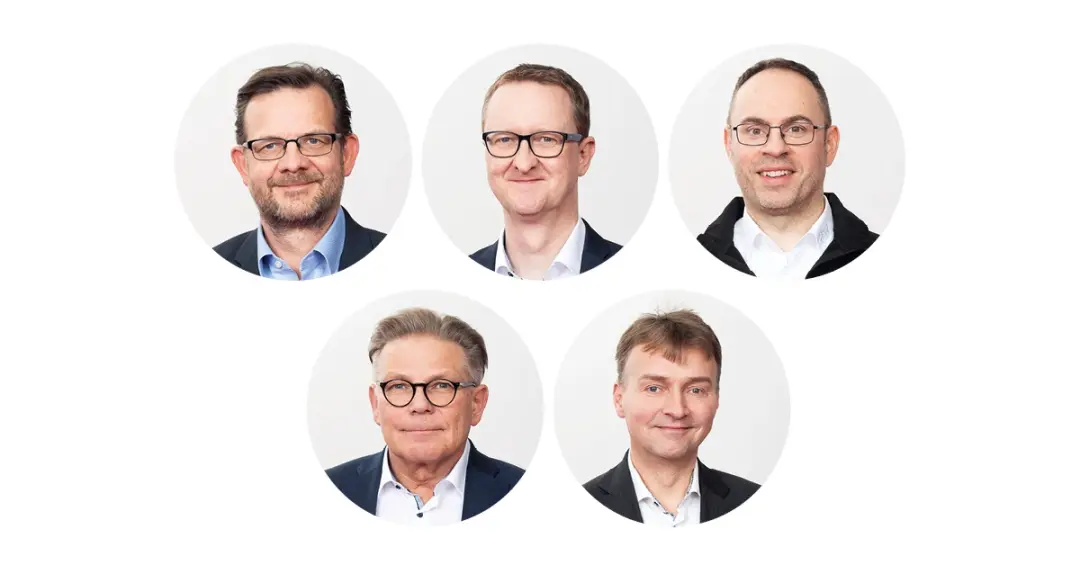
Jürgen Berger is a born and bred HELUKABEL employee and has worked at the company for 25 years. He is responsible for data, network and bus technology products.
Matthias Eick has been a global segment manager at HELUKABEL since 2014 and is in charge of automation and drive technology. Born in Lower Saxony, Germany, he’s been active in the cable sector for 17 years.
Steffen Quadt is a product manager at SEW-EURODRIVE GmbH & Co KG in Bruchsal, Germany. After completing his mechatronic dual (work-study) degree, he worked, as a drive technology engineer in the R&D of sensor technology and digital motor integration for 16 years.
Frank Sangel is the founder and managing director of Sangel Systemtechnik GmbH which became part of the HELUKABEL Group in 2022. The company is based in Bielefeld, Germany, and is a leading manufacturer of cable assemblies and system modules for machinery and plant engineering.
Martin Schleef is a business division manager of machinery and plant engineering at the Fraunhofer Institute for Manufacturing Engineering and Automation IPA in Stuttgart. The graduate process engineer worked for various international companies, including ones in the electronics sector, before devoting himself entirely to applied research.
You can also find this and many other exciting articles in the current issue #13 of our customer magazine POWER. Read it now!